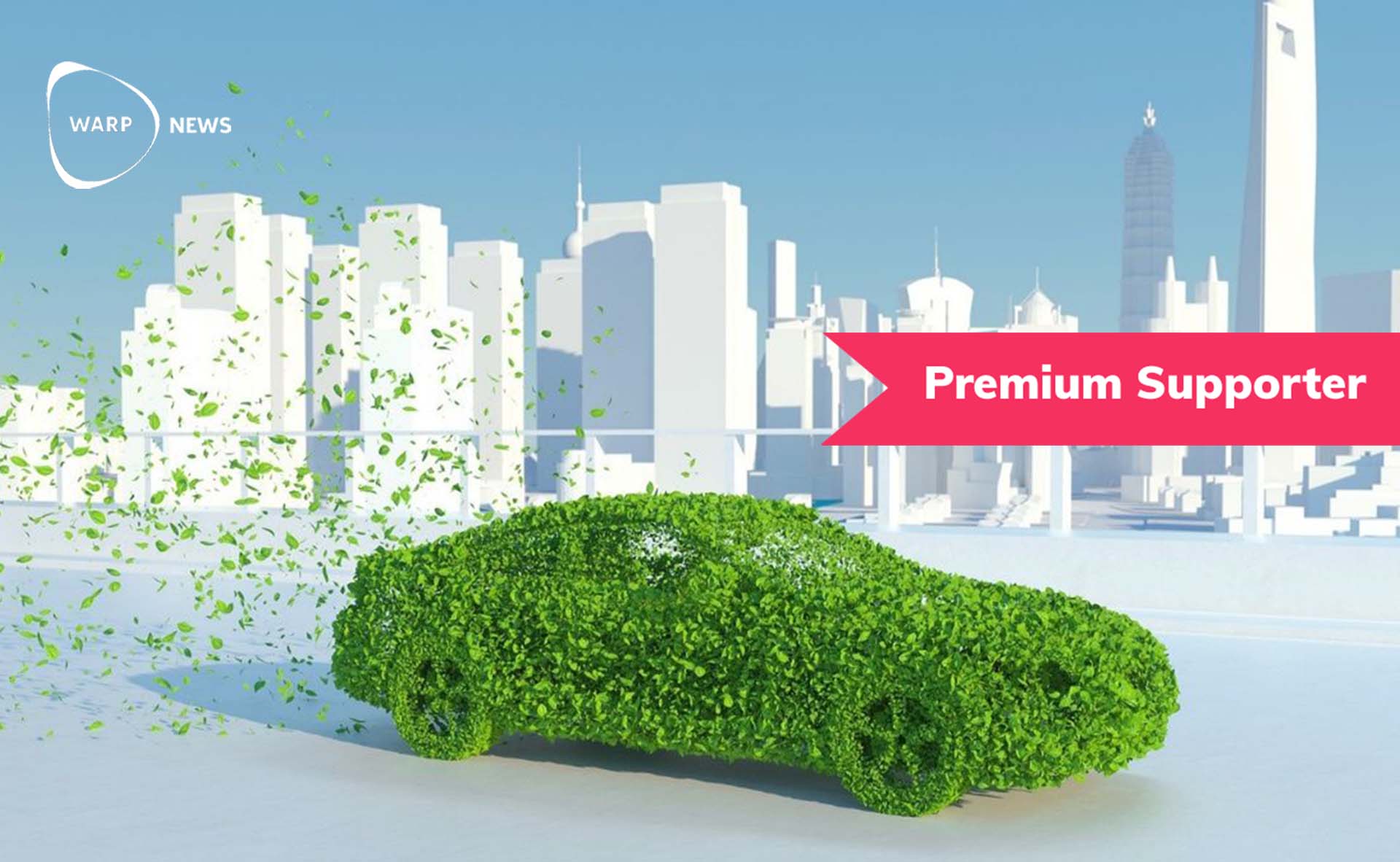
♻️ Så tar fordonsindustrin nästa steg mot hållbar produktion
Demonteringskedjor, upcycling av avfallskomponenter, bilar som tjänst och säten gjorda av återvunna flaskor – det här är den nya fordonsindustrin.
Dela artikeln
Bilindustrin dras med en rad tunga frågor: från koldioxidutsläppen som ska minskas, till ökande råvarupriser och problemet med att kassera förbrukade batterier.
En lösning som redan undersökts av många tillverkare är implementeringen av modeller för cirkulär ekonomi.
Det EU-direktivet 2000/53 har redan under en tid föreskrivit att minst 95 procent av bilens vikt ska bestå av återvinningsbart material. Begreppet återvinning av råvaror som allmänt tillämpas idag kan dock beskrivas som "downcycling", att erhålla återvunna komponenter med ett lägre användningsvärde än den ursprungliga. Till exempel återvinns bildelar vanligtvis inte i industriella processer, utan från skrotupplag, som genererar mycket lågvärdiga metallegeringar.
Å andra sidan finns det "upcycling", vilket är grundläggande i moderna cirkulära ekonomimodeller. Om vi vill skapa slutna produktionscykler måste återvinningskomponenterna ha samma värde, eller inte väsentligt lägre, än de ursprungliga. På så sätt kommer företag att kunna minska inköpsvolymerna av råvaror med både ekonomiska och miljömässiga fördelar.
Med andra ord, där återvinning syftar till att orsaka mindre skada på miljön samtidigt som linjära produktionsmodeller bibehålls, syftar upcycling till slutna produktionskedjor, vilket tar bort, eller kraftigt minskar, behovet av råvaror.
Hur fungerar upcycling?
Upcycling bygger på insikten att skrotdelar inte är ett problem som ska lösas, utan en möjlighet att ta vara på.
Först och främst, för att öka kvaliteten på skrotdelarna måste bildesign stöpas om ifrån grunden: förenkling av layouten och att planera för demonteringsskedet från första början.
Förändringar är också nödvändiga i produktionsprocessen: i fabriker bör demonteringslinjer sättas in, för att industrialisera och påskynda demonteringsoperationerna.
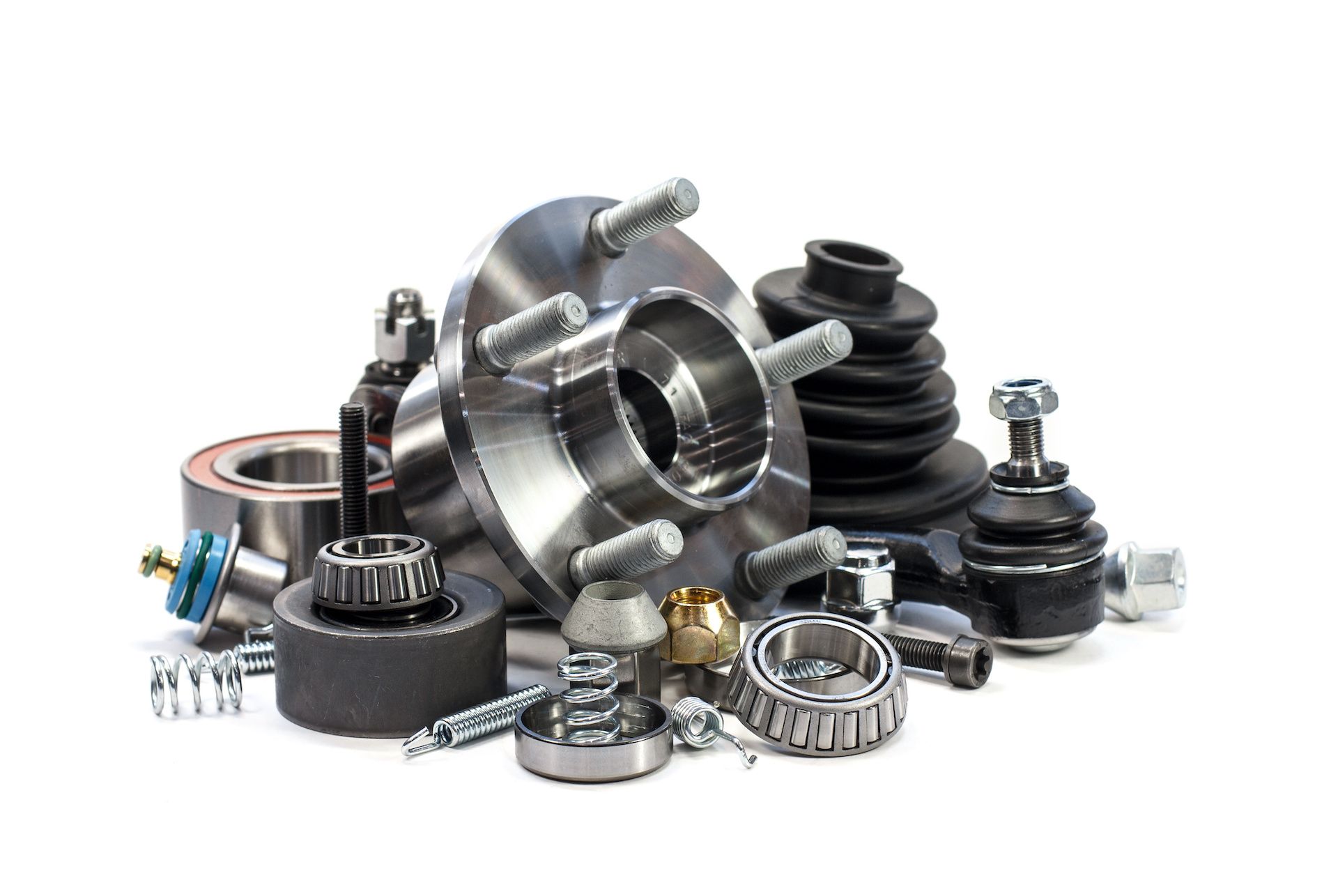
För att göra demonteringen effektiv kommer det att vara nödvändigt att bättre känna till skick på motorer och andra komponenter. Big data-eran löser detta problem genom smarta sensorer och diagnostik av fordonen.
Affärsmodeller som omvandlar produkt till tjänst kommer att vara mycket användbara i denna mening: att inte sälja bilen som ett fysiskt objekt utan som högkvalitativ service gör det möjligt för tillverkare att ha större kontroll över materia och teknik.
Det skapas också tydligare incitament att öka komponenternas livslängd eftersom bilen förblir tillverkarens egendom. Det finns flera fördelar: för kunden blir det en mer tjänste-liknande upplevelse, samtidigt som miljön gynnas av färre bilar och lägre utsläpp.
I en framtid där vissa råvaror kommer att bli allt mer sällsynta och dyra kommer återvinning som "upcycling" att bli business as usual.
Återvinning inom fordonsindustrin ingen ny idé
Men modeller för cirkulär ekonomi är inte bara framtiden.
En pionjär när det gäller att minska miljöpåverkan är ingen mindre än Henry Ford, som ju uppfann löpande bandet. Det sägs att han strax före sin död arbetade på den första fabriken som demonterade bilar.
Efter denna tankegång introducerade Henry Ford 1937 Soybean Car, en konceptbil vars kaross och fendrar var gjorda av sojabönor, vete och majs. Det var en modell som sett till konstruktionsvikt och enkelhet vida överträffade dåtidens plåtbilar. Projektet gick dock i stöpet på grund av hampaförbudet, eftersom fordonet skulle drivas av ett bränsle baserat på hampa.
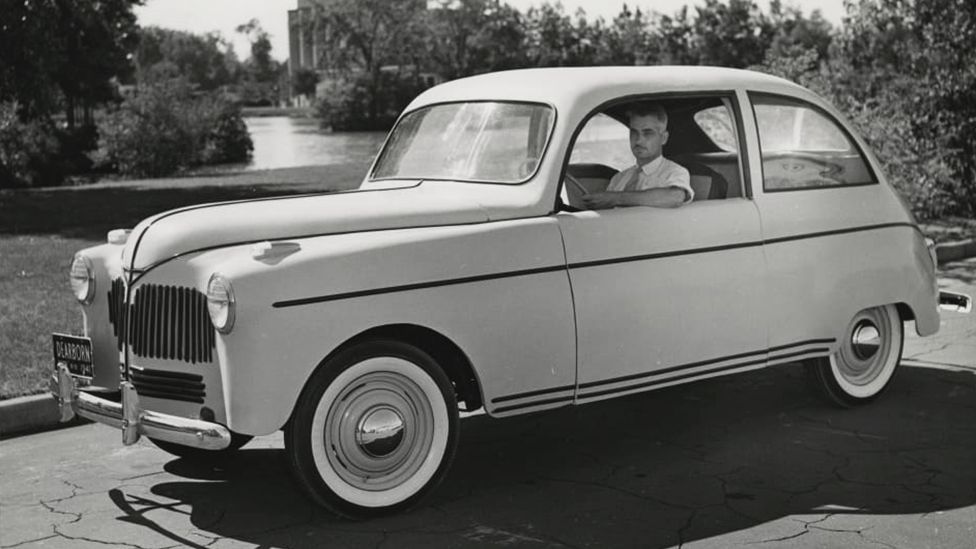
Tar vi ett stort kliv fram till 2012 hittar vi den första bilfabriken för återtillverkning som drivs av Renault vid fabriken i Choisy-le-Roi. Här demonteras motorer, mekaniska växellådor, turbos, insprutningspumpar och kasserade topplockssatser. Vissa av dessa komponenter kan genom en smart design återanvändas i nya modellers produktion. Andra tillverkas om som reservdelar till reducerat pris.
Siffror visar att Renault har minskat elförbrukningen med cirka 80 procent och avfallet med över 70 procent.
Renault kommer också att öppna en Re-Factory i Flins 2024, den första bilfabriken helt tillägnad den cirkulära ekonomin. Målen är livsförlängning, grön energihushållning och i synnerhet elbilar och högkvalitativ återvinning.
Snabb innovation inom återanvändning av däck
Låt oss stanna i Frankrike eftersom en stor investerare inom detta område är däckjätten Michelin. De har levererat däck-som-en-tjänst i flera år. Här återanvänds begagnade däck, och byggs om, samtidigt som 90 procent av det av det nya däckets prestanda bibehålls. När däcket inte längre kan repareras blir det högkvalitativt regenererat gummi eller etanol, som båda kan återanvändas i produktionscykeln.
För närvarande försöker Michelin, i samarbete med Carbios, göra de första 100 procent hållbara däcken. Den innovativa enzymatiska återvinningstekniken som de har utvecklat gör det möjligt att erhålla gummi från återvunnen PET från flaskor, klädfibrer och så vidare.
Denna teknik använder ett enzym som kan depolymerisera PET totalt, vilket kan återanvändas som sekundärt råmaterial med samma egenskaper som jungfruligt material.
Processen har validerats och avsikterna är att tillverka de första däcken exklusivt av återvunnet material till 2050.
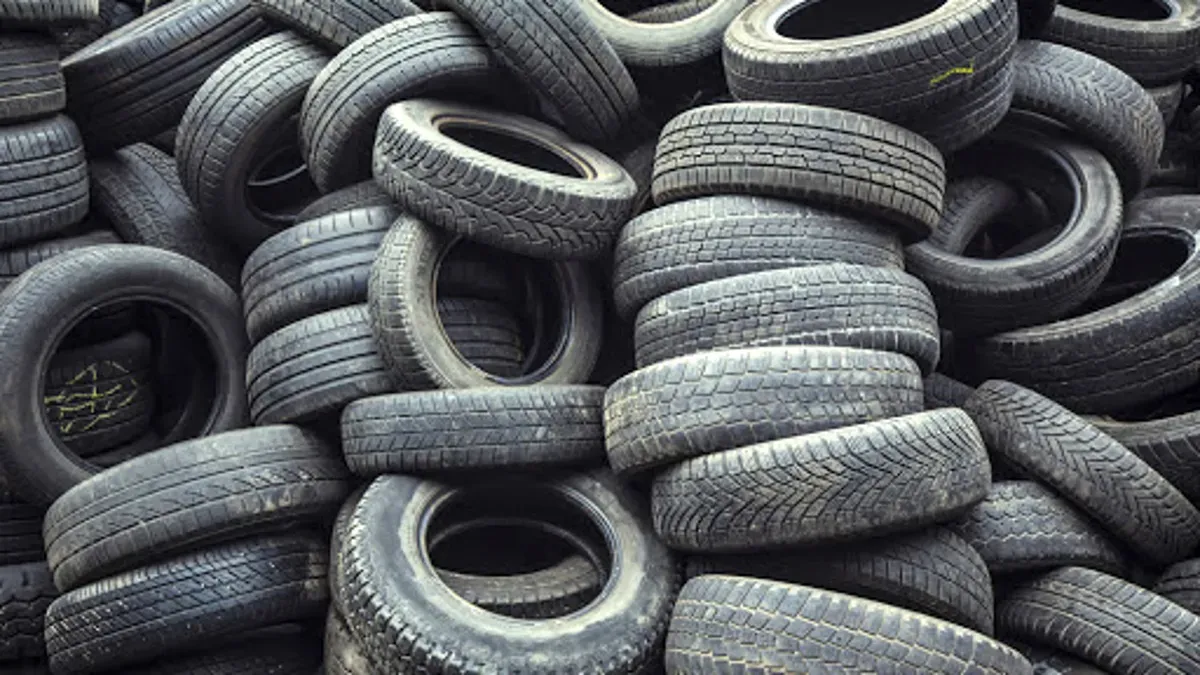
Ett annat exempel är amerikanska PRTI, eller Product Recovery Technology International, som i sin process tar tillvara på gamla däck och återanvänder dem eller använder dem för energiproduktion. Allt med mycket låg miljöpåverkan.
Slutna cykler kräver revolutionerande idéer
Resan mot avancerad upcycling inom bilindustrin kommer till Tyskland. En tillverkare som satsar hårt på den cirkulära ekonomin är Audi som sedan 2019 startat en rad projekt för att stänga sina produktionscykler.
Audi är redan igång med projektet "Aluminum Closed Loop" för att återanvända aluminium, ett material som har stor betydelse för dess bearbetning. Återvunnet aluminium som håller samma kvalitet som jungfruligt material används för tillverkning av komponenter, vilket resulterar i en 95 procentig minskning av energiförbrukningen.
Ett annat projekt syftar till att tillverka bilinteriörer med PET som återvinns från flaskor. Detta kräver en komplex produktionsprocess, där flaskorna krossas till granulat som i sin tur används för att skapa polyestertrådar och plastgarn. Interiören i nya A3 Sportback är redan till 89 procent gjord av återvunnet material med identisk textur och utseende som originalet.
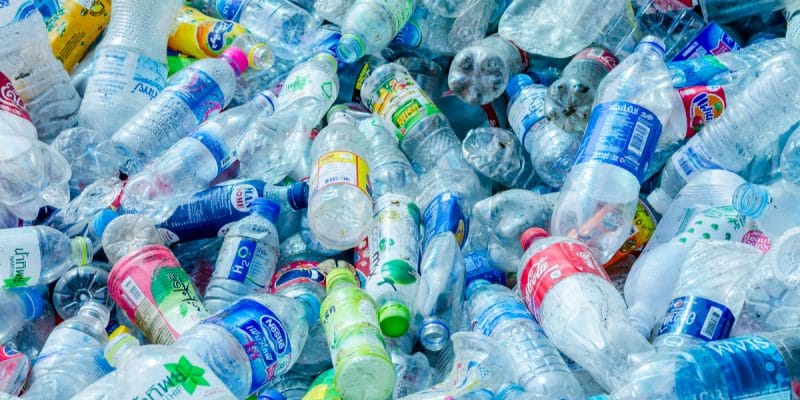
Ett särskilt innovativt projekt lanserades nyligen i samarbete med Karlsruhe Institute of Technology. Många plaster är inte återvinningsbara med nuvarande processer, särskilt de som tillverkas med en blandning av polymera råmaterial. Återvinningen av dessa avfallskomponenter studeras genom kemisk återvinning. Denna process gör det möjligt att erhålla pyrolysolja som kan användas i produktionscykeln av komponenter istället för petroleumprodukter, med liknande kvaliteter.
Slutdestination: Elbilen
Elmotorn är en väsentligt enklare konstruktion än förbränningsmotorn: den har färre komponenter och färre rörliga delar. Därför är den, förutom att vara effektivare och mindre förorenande, också mer lämpad för återtillverkning eftersom den är lättare att demontera.
Det här är ytterligare bekräftelse på att framtiden tillhör det elektriska.
Effektiva lösningar för återvinning av tungmetaller, som litium, från batterier är på gång. Idag uppskattas uppskattas att mindre än 5 procent av dessa material återvinns idag, dessutom genom processer med hög effekt. Men det forskas ivrigt inom området, inklusive tillverkare som Audi och Renault.
Ett särskilt intressant projekt pågår vid Coventry University där en forskargrupp ledd av proffessor Farnaud undersöker återvinningen av litium genom biolakning.
Det är en naturlig process, som använder bakteriearter, som Acidithiobacillus ferrooxidans, som naturligt "matar", oxiderar och extraherar tungmetaller som en del av deras ämnesomsättning. De erhålls i grödor vid 37 °C utan behov av höga temperaturer eller giftiga kemikalier och därför med mycket låga utsläpp.
Ett annat exempel är Svenska Northvolt som har producerat den första battericellen med 100 procent återvunnet nickel, mangan och kobolt och nu siktar på att skala upp processen.
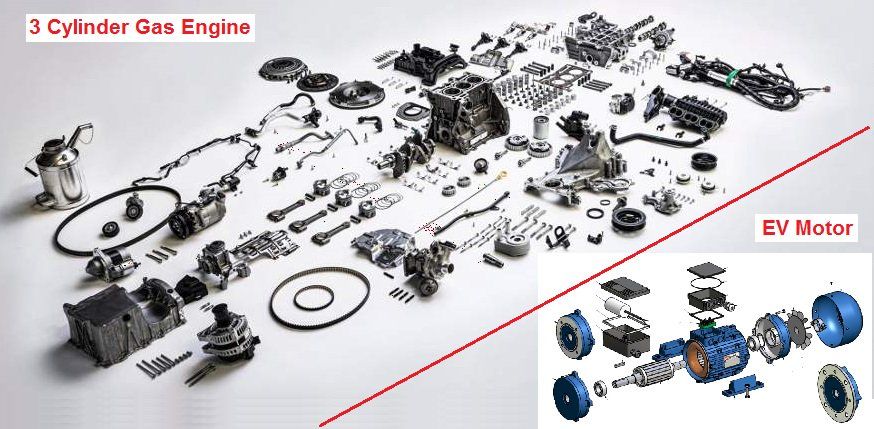
Forskningen pågår och är ytterligare en pusselbit i det vi ser hända: 2025 uppskattas det att elbilar kommer att vara både billigare, även i inköp, och bättre än sina förbränningsdrivna motsvarigheter. Dessutom kommer de till stor del att bestå av återanvänt och återvunnet material. Kort och gott bättre, både för människor och planet.